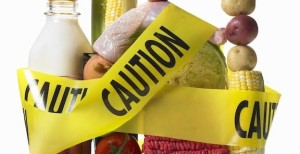
As a concerned parent, I certainly pay more attention to product recalls now than, say, six years ago. But it also seems like product recalls are making the headlines a lot more often these days. This is due in large part to contamination outbreaks in the food and beverage industry. These recalls are often voluntary, as the producer discovers E. coli or other food-borne illnesses in their products. However, if the company refuses to recall these foods, the FDA and FSIS have the authority to detain and seize those foods in commerce. The FDA has
three classifications of recalls for all food products (except meat, poultry, and eggs). Due to the backlash of recent outbreaks, however, the majority of recalls are voluntary.
There have also been a number of recalls due to child safety concerns, most notably with toys and child safety seats. Again, the majority of these recalls are also voluntary. And quite often, there have been no reported injuries or deaths resulting in the recall. While consumers head to stores in droves to return these products, one thing probably doesn’t cross the mind of most people in the process – the ridiculous hassle of managing all of these returns.
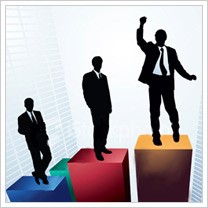
As I’ve mentioned numerous times before, at the end of last year, Clint Reiser and I worked on an extensive survey examining the omni-channel commerce landscape. As part of the survey, we asked participants a series of questions about a few key performance metrics. These metrics looked at both financial and operational performance. We decided to separate out the respondents into two groups: top performers and bottom performers based on their performance. The top performers were defined as those organizations with 10+% year-over-year revenue growth as well as 95+% on-time order fulfillment rates. One of the differentiating technologies that top performers used was reverse logistics. . We consider reverse logistics to be a robust returns processing system.
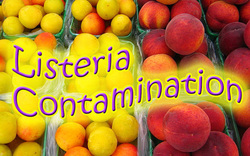
Reverse logistics plays a huge role in product recalls. And the type of role it plays is based largely on the type of product recall. For contaminated food, for instance, it could be as simple as a straight return and credit processing project. Here, the store needs to track the returned item and credit the customer’s account, whether that is a cash return or the amount is credited back to a payment card. For other types of recalls, such as child safety seats, the return is also pretty straight forward. The customer returns the product, whether that is to a store or they ship it back to the manufacturer. The manufacturer processes the return and swaps out the defective product for either a new version or a comparable version. This is also on the easier side of product returns, except for the large volume of returns and the processes required to track all of the returns.
Consumer electronics can pose a more complex return process. This is especially true if the product is going to be refurbished and then shipped back out to the customer, or made available to another customer. These product returns still need to be tracked and processed. After that process, the refurbished product can be made commercially available again. A reverse logistics engine allows companies to achieve this. By efficiently re-entering returned and refurbished merchandise into the inventory stream, the company can recoup some of the losses of the initial return.
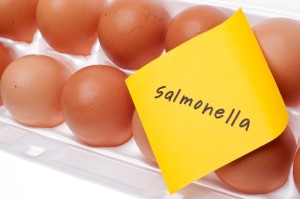
The key to minimizing damage, both in the form of bad publicity and lost profits, is effectively managing product recalls. In order to do this, companies need to plan for the unfortunate event. First, they need a process to determine if a recall is needed. Second, they need to determine the best way to communicate the recall. Getting ahead of bad publicity is huge. Third, they need to determine where items can be returned. This can be to stores, warehouses, or having the product shipped back to a variety of locations. Finally, they need to know what to do with the item. If it is a perishable item with food-borne illnesses, the product will need to be disposed of properly. For other products, such as child safety seats and consumer electronics, the product may simply need a minor repair. Having these plans in place ahead of time saves time and money. By having a reverse logistics application in place, companies can streamline and automate the majority of this process. And in the process, they can alleviate some of the headaches that go along with product recalls.
No comments:
Post a Comment