5 Key Metrics to Monitor, Benchmark and Optimize Transportation Spend
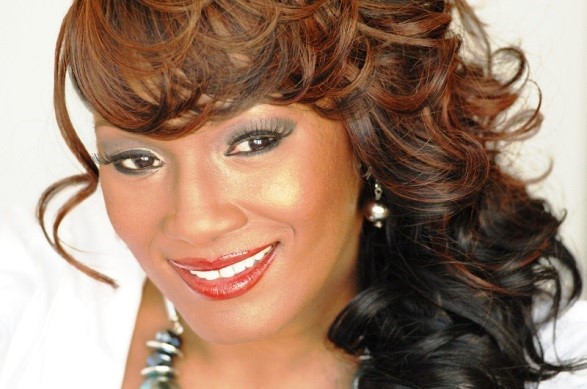
Complexities such as:
- What exactly am I spending today?
- Who exactly are my best carriers and how can I work with them better?
- How effective is my current transportation strategy and where am I missing the mark?
- What are the right things to measure to really understand where my transportation strategy is today while getting insight into where it needs to be?
These complexities underscore a mounting concern faced by logistics executives to balance the competing pressures of both cost and service in today’s end to end supply chain. When looking at the pressure around finding this balance, two elements have been highlighted in our conversations with executives as the top two pressures. The first is fuel cost and volatility while under the pressure to compete. The second is a heightened awareness of the general cost and service impact transportation overall has on the business as a whole.
The external pressure of fuel costs and volatility may leave many executives feeling somewhat limited in terms of their ability to control or impact that variant. Combine that feeling with the sensitivity of the general bottom line cost impact to the business and you have a recipe for losing a good night’s sleep. Let’s take a closer look at what to measure and a simple action item that could shift this dynamic at your company.
Here are five key metrics to monitor, benchmark and optimize transportation spend for your business:
- Change in baseline freight spend year over year?
- What percentage of your carriers are compliant in contract?
- What percentage of your carriers are meeting their service level and routing compliance needs?
- What is your average time to process and pay a freight invoice?
- What percentage of your transportation invoices are currently audited?
By simply beginning to review and monitor these five KPIs, your company will be well on the way to not only optimizing costs, but to better understanding the variable influences and fluctuations of your transportation costs. You will begin to get a clear picture of where the real weaknesses are and which of your carriers are the best partners of your Supply Chain.
However, by utilizing dock scheduling, shippers can reduce carrier wait time and accidents while increasing visibility and optimizing resource planning. I’d like to share a deeper look at the role that dock scheduling plays in not only optimizing costs, but also in automating business. Long waiting times for pick-up and delivery are costing U.S. shippers, carriers and consumers millions of dollars every year. Prior to 2013, truck drivers were allowed to work 82 hours a week. Federal rules have changed reducing these hours to 70 per week. Drivers can complete no more than 14 hours for any shift and may not drive more than 11 hours during the shift. This dynamic really adds to the pressure felt by the executives to balance an already precarious Supply Chain. Dock Scheduling can uncover and enable efficiencies at the dock, enabling carriers, shippers, 3PL’s, and warehouses to coordinate carrier schedules with load and dock availability. By then utilizing multiple communication channels, the driver is allowed to maximize his 70 hours, enabling the required rest period while still providing delivery in a timely manner.
Using the requirements of the specific dock of delivery, Dock Scheduling enables the warehouse or shipper to stage their loads in order of pick-up or delivery while communicating with the carrier company and the specific driver of any loading dock issues. This level of optimization leads to greater efficiencies which produces substantial results.
All parties are able to seamlessly and effectively communicate throughout the entire process. This enhanced communication and visibility enables a faster close loop process of the entire shipping, delivery and reporting process resulting in:
- Reduced idle times at loading and unloading by 20 – 40% thus lowering fuels costs
- Increased loading/unloading productivity by 20% +
- Clarity in the loading-unloading process
- Decrease of transportation’s overall impact on the business
The key takeaway is to understand what to measure and monitor, understand their influences on your transportation costs and to take action by moving forward with the visibility and automated collaborative insights that Dock Scheduling can bring to your company. Five measures, one step forward with Dock Scheduling and your business will be on the way to experiencing significant spend optimization like TRANSPOREON Group customers, Vinnolit, Swiss Steel and more.
No comments:
Post a Comment