Getting Accurate Offshore Supplier Audits is Not Easy
Auditing suppliers, especially in low cost countries, to ensure compliance with various standards a company may have for safety, treatment of workers, environmental practices and more is all the rage these days, led by companies such as Apple and Walmart.
The practice really took off in 2012, after a series of disasters in apparel factories in Bangladesh and Pakistan led to the deaths of hundreds of workers in those countries.
|
So many Western companies have hired firms to audit is suppliers to assure themselves and their customers that their suppliers are behaving properly.
Oh that it were that easy.
An interesting article in the UK's Supply Management magazine highlights many of the challenges such audit programs have. Consider that suppliers can potentially lose millions of dollars as the result of a poor audit, and you can imagine the lengths to which they might go to ensure the report is favorable.
Start with payroll records, which might show a factory was burdening workers with excessive overtime, not paying them fairly, and more. Those companies may attempt to fudge the payroll data that is provided to Western companies, and there is at least one Chinese firm that openly advertises it provides software to create fake factory accounts by altering payroll records for inspection.
Of course, with upfront warning of an inspection or audit, factory owners may move fast, ordering managers to unlock fire doors and clear blocked stairways.
"Machinery will be moved into containers parked outside the factory, so it does not appear overcrowded," the article notes. "Child workers will quietly leave by the back door when a certain piece of music is played over the PA. Charts setting out health and safety requirements may well be moved from one factory to the next to keep one step ahead of inspectors."
Managers, of course, will be coached on what to say about wages, benefits, working hours and other practices. Ditto for employees, where owners likely have handpicked specific workers to talk with the inspectors (some companies such as Apple force owners to allow them to talk with any worker they want.
That's all if the inspectors are in fact actually being shown the factory that makes the Western company's products.
"Quite often you get suppliers who will say they'll take you to their factory, but in production they could be using a completely different one," says Amanda Lockley of product-sourcing firm Matrix APA, which makes regular site visits to all its suppliers. "It's quite easy, especially if there's no name or if it's a Chinese name outside, to say: "This is the factory" - but it could be just a show factory."
A similar trick involves secret sub-contractors to the company being audited. Factory owners may have finished goods sent to the approved factory's packing area for the inspection and then returned to the subcontractor for shipping, which the magazine says is a "growing problem," especially in Turkey.
Savvy factory owners have learned other tricks, such as spending lots of time in general conversations, going to a restaurant for long meals, taking a circuitous route to the destination - all geared to minimizing the amount of time spent in the factory itself or talking to workers.
Then of course there is the risk of factory owners simply bribing the inspectors - at a far lower cost than losing the orders from Western companies or changing business practices.
And in some cases, Western companies may be getting so focused on these social and sustainability issues that they are perhaps putting less attention than they should to core product quality.
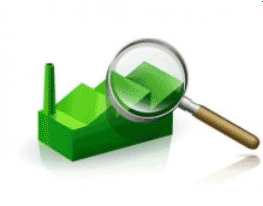
And while a few mega-companies may have the resources to conduct audits deep into a multi-level supply chain, they are the exceptions.
One answer may be come from more collaboration by Western companies, certainly non-competitive firms but maybe even with competitors in the not too distant future. Why should many different firms all audit the same suppliers, which is not only expensive but creates "audit fatigue" at the vendors.
When hiring an audit company, or planning for a supplier audit, there are many questions that need to be answered.
For the auditing firm, do they speak the local language well? What is their approach to the audit process? What kind of training and experience of investigation do they have? Do they simply carry out desktop research or do they physically audit? If they are auditing working conditions, do they use their staff or rely on third parties in the relevant country?
For a given audit, questions include how big is the factory to be visited? How long does a reliable audit take? One day? Three? How many inspectors should there be? One? A team? What exactly are they to examine?
Put all this together, and the supplier audit process is rife with challenges and risks. More collaboration on the efforts seems like the one clear answer to in part address these many issues.
No comments:
Post a Comment