Supply Chain News: Non-Putaway Distribution Models Improve DC Productivity by Eliminating a Pallet or Carton Touch
From Merge-in-Transit to DC Pypass and of Course Cross Dock, We Describe and Illustrate the Opportunities
Many companies track "touches per pallet" as one way to measure distrubution center productivity.
It makes perfect sense: the fewer times on average DC workers handle a pallet or carton on its way from receipt to customer, the lower the total cost of such handlling should be.
|
One way to drive that metric down would be to use distribution processes that have been designed to eliminate a touch or two. So-called "crossdocking" is perhaps the most obvious example of this, but there are a number of others, as we describe below.
Distribution Cross Dock: Product that is received in one door is taken directly to staging/outbound doors without re-packing or value-added services. This approach generally requires an advanced shipping notice and a pre-allocation of the incoming goods to specific customers or retail stores. Warehouse club retailer Costco, for example, is said to cross dock 80% or more of its inbound receipts, a task made easier because it mostly handles and cross docks full pallet loads from suppliers.
It can work well for retailers, which often have a "door per store" operation, and is often done using conveyor systems to move the cross docked cartons. But has proved much harder to achieve outside of retail, where there are timing issues relative to merging cross docked products with goods picked from stock needed for a given order.
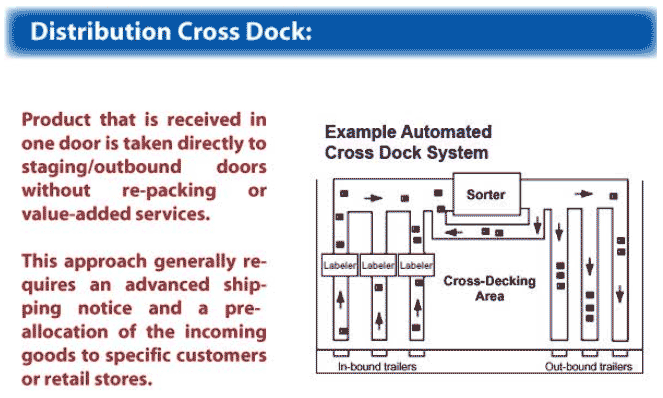
Manufacturing Cross Docking: Product is taken directly to staging/shipping from production lines. This can be true for internal shipments (plants to a company’s own DCs) or to a customer. This obviously requires that product allocation to DCs/customers be known at the time of production. Typically, a pallet of goods receives a serialized bar code, and when identifier is scanned into the Warehouse Management or other system, it directs workers where to take that pallet. SABMiller, for example, even has rail lines running right into some of its plant DCs, and takes palletized cases of beer straight from the production line into rail cars or truck trailers in some cases, meaning the pallet is loaded in just one touch.
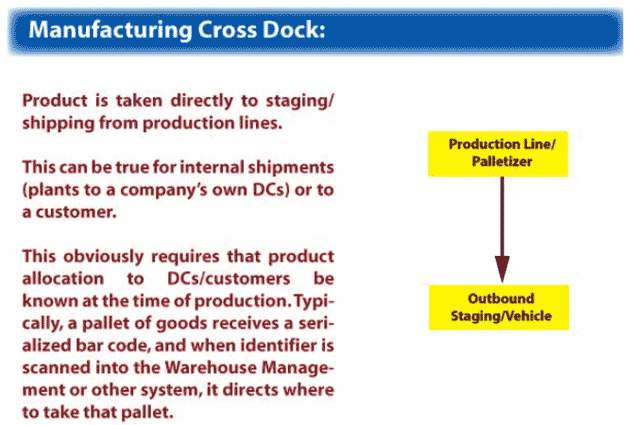
Flow Through: Similar to distribution cross dock, except that it implies some level of repacking or value-added services are involved between receipt and shipping. So, for example, full pallets are brought in, and operators break those pallets down and rebuild mixed-SKU pallets for outbound shipping. In retail, price ticketing or other services may need to be executed for the received goods. The key is that the products involved in flow through are never actually putaway for later picking before they are sent to staging or right into outboud trailers.
In Europe, there is a unique practice of flow through not found in the US. Some large retailers, such as Tesco and Carrefour, include in their networks focused distribution facilities that start each day empty or nearly so. At the start of the day, pallets are placed on the floor, and as incoming goods are received, operators drive to the different pallets on the ground, and put cases on the appropriate floor pallets until their pallets are depleted. After all receipts are processed, the pallets are loaded for store delivery and, at the end of the day, the DC is empty again.
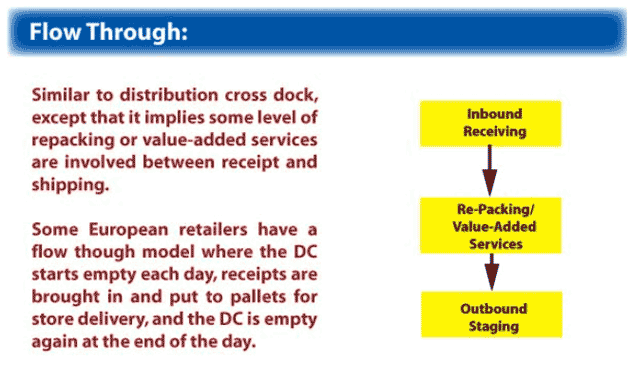
In reality, the terms cross dock and flow through are often used somewhat interchangeably and, in some cases, both processes as formally defined are used in the same facility. For example, a retailer might directly cross dock a given percent of receipts, and do re-packing/services on another portion (flow through). In neither case is the received product put away into storage for later picking, though of course, many/most DCs also use traditional putaway and order picking in addition to cross dock/flow through in those operations.
DC Bypass: A concept that has been talked about thus far more than actually used, it involves receiving product sourced internationally into import warehouses, where it is sorted and transloaded for shipment directly to customers without going to the importing company's own DCs first and the handling required there. Generally focused on goods heading to retailers. There is a related version of this where say a 3PL in China would pack goods specifically for specific retail stores in the US, but that idea has not much caught on either.
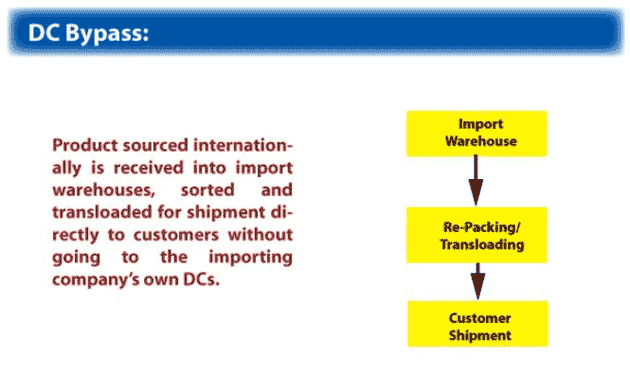
Plant Direct Shipments: Similar in a sense to DC Bypass, product is shipped to customers directly from manufacturing plants, rather than from distribution centers, eliminating significant distribution costs. The downside is that it may result in multiple shipments/deliveries to a customer for each order, if each plant does not make all items (usually the case). Plant direct shipments could be used with manufacturing cross docking, but usually the product is first stored in a plant warehouse and then shipped. Tire maker Michillen recently began using plant direct shipments for some orders after it segmented its supply chain into four different delivery models, versus before when everything went from a company DC to a distributor's DC and then to the final customer.
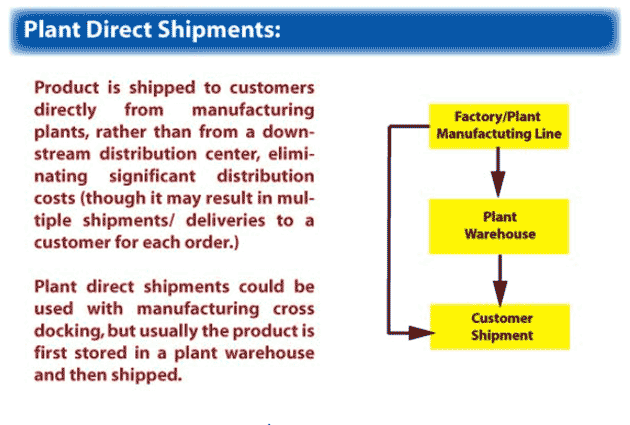
Merge-in-Transit: Goods from multiple sources for an order (a company’s own factories, outside suppliers) are sent to a special type of distribution center, where they are consolidated for shipment. The traditional example cited for merge-in-transit is for PCs, where the manufacturer needed to mix locally-produced computers with monitors, keyboards, printers, etc., produced by others. There is also an international version, in which bulk shipments from different sources are merged and sent to customers, such as large reseller channels, as one shipment. Timing and synchronization are the key challenges of merge-in-transit, and usually storage areas close to receiving/shipping are needed to hold the earliest arriving inventory. Strong WMS support is required, as 3M found out in the early 2000s when a merge-in-transit strategy initially failed due to the inability of the then-current WMS to manage it well enough.
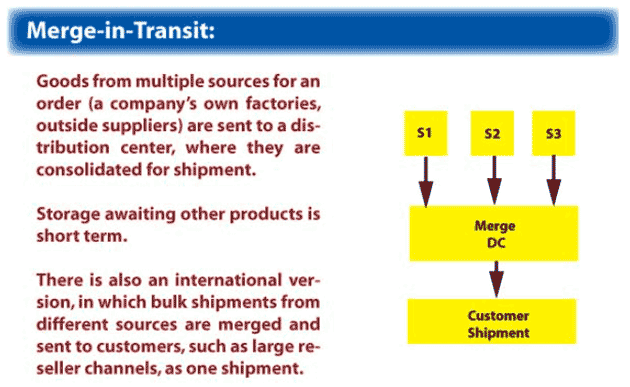
ReplyDeleteThis is really very informative and very detailed blog. Thank you so much for sharing this post, Ir really helped me a lot to understand that what is inventory and strategy for it.inventory management marketing materials.DLXpress is Best Delivery Service in CA , USA . know more about me. visit here - www.dlxpress.com